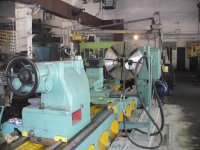
Анализ большого количества технологических проектов, выполненных для обрабатывающих центров и станков с ЧПУ в серийном производстве, показывает, что:
стоимость обработки (оперативного времени) составляет около 80% от всех затрат;
стоимость инструмента не превышает 3-4%;
стоимость замены инструмента не превышает 1%.
В результате такого анализа можно сделать вывод, что:
сокращение затрат на приобретение инструмента на 30% (например, за счет сокращения закупочных цен) сокращает затраты на механическую обработку на 1%;
сокращение времени замены изношенного инструмента на 50% (что соответствует двукратному увеличению стойкости) снижает затраты на 1%;
увеличение производительности (сокращение времени обработки) на 20% сокращает стоимость обработки на 15%.
Как уже было указано, при неизменности стоимости станко/часа сокращение затрат определяется сокращением времени. Для определения путей сокращения времени обработки надо определить основные составляющие оперативного времени и затем определить технические и организационные пути его сокращения. Аналогично определяются пути сокращения времени наладки.
Совокупность целого комплекса технологических мероприятий, направленных на повышение эффективности механической обработки за счет повышения ее производительности, носит название высокопроизводительной обработки.
Основная цель высокопроизводительной обработки – повышение эффективности обработки резанием путем увеличения объема удаляемой стружки в единицу времени. Предполагаемое повышение составляет до 500%.
В отличие от высокоскоростной обработки, подразумевающей большие частоты вращения (скорости резания) при малых подачах и малых глубинах обработки, высокопроизводительная обработка предполагает увеличение подачи и глубины резания при одновременном не столь значительном увеличении скорости резания.
При переходе на высокоскоростную обработку практически всегда требуется замена оборудования. Кроме того, обязательно требуется изменение организации технологического процесса, введение обязательной балансировки применяемого инструмента, применение дополнительных средств безопасности.
Высокопроизводительная обработка в большинстве случаев может быть реализована на существующем в производстве оборудовании с ЧПУ путем оптимизации инструмента и режимов обработки.
Область применения высокопроизводительной обработки лежит в черновом резании деталей из серого чугуна и цельных конструкций из легких сплавов в авиационной промышленности. Эта область может быть расширена за счет обработки серийных деталей из легких сплавов. Увеличение производительности достигается за счет применения комбинированных инструментов, высоких подач и скоростей резания. В результате реализуется совмещение переходов и резкое увеличение объема удаляемой стружки.
Высокоскоростная обработка реализуется за счет применения оборудования с высокими частотами вращения шпинделя и применения на этом оборудовании оптимизированных с точки зрения твердого сплава и покрытия инструментов. Высокопроизводительная обработка предъявляет определенные требования к оборудованию. Станок должен обладать высокой мощностью шпинделя, хорошей динамикой приводов и систем ЧПУ, высокой статической, динамической и температурной жесткостью, высокими скоростями позиционирования исполнительных органов, обеспечивать хороший отвод стружки.
В результате реализации высокого удельного объема удаляемой стружки достигается сокращение оперативного времени при одновременном сохранении и повышении гибкости процесса. В итоге потребитель получает сокращение затрат на обработку, повышение производительности и сокращение сроков поставки оборудования.
Одним из обязательных элементов системы сокращения затрат является организация инструментального хозяйства. Сокращаются затраты, связанные с наладкой и оперативным временем. Система организационно-технических мероприятий, направленных на поддержание оптимальных запасов инструмента в оптимальном техническом состоянии, называется инструментообеспечением – tool management. Эта система решает следующие основные задачи:
подготовка инструмента;
предварительная настройка инструмента;
балансировка высокоскоростного инструмента;
средства ухода и вспомогательные материалы;
восстановление режущих свойств;
организация переточки инструмента;
восстановление износостойкого покрытия;
упаковка;
организация хранения и учета;
организация складского хранения;
утилизация инструмента.
В зависимости от степени проработки системы инструментообеспечения существует несколько вариантов ее реализации. На первой ступени фирма, отвечающая за инструментообеспечение, занимается только поставками инструмента по спецификации, выданной потребителем. На второй ступени добавляется ответственность за правильный подбор инструмента. На третьей ступени поставщик услуги инструментообеспечения доставляет инструмент к станку, осуществляет техническую поддержку производства, управляет складом и отвечает за постоянное улучшение технической и экономической составляющей. На четвертой ступени поставщик услуги содержит у потребителя бригаду своих сотрудников для решения вопросов на месте и для детального и быстрого анализа отказов. Оплата его труда осуществляется по количеству и сложности работающих инструментов. На пятой, последней, ступени поставщик услуги отвечает за восстановление режущих свойств инструмента, его настройку вне станка, оптимизирует процесс обработки таким образом, чтобы стоимость обработки была минимальна. Оплата его труда осуществляется в зависимости от количества выпущенных деталей, т.е. оплачивается определенная сумма с каждой выпущенной детали.
Реализация указанных выше особенностей современного производства позволяет существенно повысить его эффективность независимо от области реализации продукции.