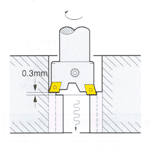
По теме растачивания написано множество статей как очень качественных, так и вводящих в заблуждение. Для эффективного выполнения этой важной операции необходимо развеять существующие мифы.
Растачивание — это внутренняя токарная обработка. Расточные операции сводятся, как правило, к получистовым и чистовым. Для растачивания используются расточные резцы.
Расточной резец состоит из трех основных частей: сменной неперетачиваемой пластины, тела расточной оправки и хвостовика. Хвостовик — это часть расточной оправки, по которой ведется ее базирование и закрепление. Обычно длина закрепления равна четырем диаметрам оправки. Расстояние от хвостовика до пластины, т.е. незакрепленная часть резца, называется вылетом.
Вылет определяет максимальную глубину растачивания и является самым важным размером расточного резца. Слишком большой вылет вызывает избыточные упругие деформации расточной оправки, способствует появлению вибраций, которые ухудшают качество поверхности, и может привести к преждевременному износу пластины.
Для большинства операций необходимо выбирать расточную оправку с максимальной статической и динамической жесткостью. Статической жесткостью оправки называют ее способность противостоять упругим деформациям (отжиму) под действием силы резания. Динамическая жесткость оправки определяется ее способностью гасить вибрации.
Сила резания
Силу резания, действующую на расточной резец, легко измерить. Она включает в себя три составляющие: тангенциальную, осевую и радиальную. Тангенциальная составляющая силы резания имеет наибольшее значение. Она направлена перпендикулярно передней поверхности пластины и обеспечивает отжим резца в вертикальной плоскости. Важно отметить, что тангенциальная составляющая силы резания приложена к вершине режущей пластины и не проходит через ось оправки. Таким образом, если у силы есть плечо, появляется момент, который закручивает оправку относительно ее оси.
Вторым по величине значением обладает осевая составляющая силы резания, но действует она параллельно оси оправки и, следовательно, не вызывает отжима. Радиальная составляющая силы резания направлена перпендикулярно оси оправки и вызывает отжим.
Таким образом, только тангенциальная и радиальная составляющие силы резания вызывают отжим расточного резца. Десятилетиями считалось, что осевая и радиальная составляющие силы резания равны 50 и 25 процентам от тангенциальной соответственно. На сегодняшний день это соотношение представляется неверным, так как оно в большой степени зависит от обрабатываемого материала, его твердости, условий резания и радиуса при вершине режущей пластины.
Отжим расточного резца
Анализ формул для расчета отжима расточного резца и момента инерции поперечного сечения оправки показывает, что следует руководствоваться следующими правилами при выборе инструмента для растачивания:
Вылет расточного резца должен быть минимальным. При увеличении вылета отжим увеличивается. Например, при увеличении вылета в 1,25 раза, отжим увеличивается в 1,95 раза при неизменном диаметре оправки и остальных параметрах.
Диаметр расточного резца должен быть максимальным. При увеличении диаметра оправки увеличивается момент инерции поперечного сечения и отжим уменьшается. Например, при увеличении диаметра оправки в 1,25 раза, отжим уменьшается в 2,44 раза ( ) при неизменном вылете оправки и остальных параметрах.
Чем выше модуль упругости материала оправки, тем меньше отжим при неизменном вылете и диаметре оправки и остальных параметрах.
Материал оправки
Расточные оправки делают из стали, тяжелых сплавов на основе вольфрама и твердого сплава. Наиболее популярным материалом является легированная сталь, но некоторые производители используют и углеродистую сталь. Вне зависимости от марки все углеродистые и легированные стали обладают одним и тем же модулем упругости, МПа. Распространенным заблуждением является то, что оправка из стали с большей твердостью или прочностью лучше противостоит упругим деформациям. Как видно из формулы для расчета отжима при растачивании, он не зависит от твердости или прочности материала, а зависит от модуля упругости.
Тяжелые сплавы на основе вольфрама получают методом порошковой металлургии из порошков вольфрама, никеля, железа и меди и др. Модуль упругости таких материалов МПа. Отжим оправок из этих материалов на 50-60% меньше чем у стальных при одинаковом вылете и диаметре оправки и остальных параметрах.
Расточные оправки из твердого сплава обеспечивают наименьший отжим благодаря высокому модулю упругости. Обычно расточные оправки из твердого сплава состоят из 90-94 процентов карбида вольфрама и 10-6 процентов кобальта, соответственно. Модуль упругости таких твердых сплавов МПа.
Материалы и геометрии режущих пластин
Режущие пластины для растачивания изготавливают из различных материалов: твердого сплава, керамики, кермета, поликристаллического алмаза и кубического нитрида бора.
На твердосплавные пластины наносят покрытия химическим или физическим методом. Примером покрытия, нанесенного физическим методом является TiN, которое подходит для обработки жаропрочных сплавов и аустенитных нержавеющих сталей и TiAlN, которое широко используется для большинства сталей, титановых сплавов, серого чугуна и цветных металлов.
Эти два типа покрытия наносятся на карбидные основы, которые обладают высокой температурной стойкостью и стойкостью к выкрашиванию. Карбидная основа как правило состоит из 94 процентов карбида вольфрама и 6 процентов кобальта. Такие сплавы соответствуют группам применения по ISO K10-K20, M10-M25, P10-P20.
Твердосплавные пластины с химическим нанесением покрытия используются для обработки большинства сталей и чугунов. Химически наносимые покрытия — это многослойные сочетания TiN, оксида алюминия, TiCN и TiC. Каждый слой служит определенной цели, а комбинации слоев обладают стойкостью к различным видам износа. Типичными твердыми сплавами являются сочетания карбида вольфрама, тантала и титана и кобальтовой связки. Такие сплавы соответствуют группам применения по ISO K10-K30, M10-M45, P05-P45.
Режущие пластины из керамики изготавливают на основе оксида алюминия Al2O3 и нитрида кремния Si3N4. Керамика на основе оксида алюминия изготавливается без покрытия или с покрытием, наносимым физическим методом. Непокрытая керамика обладает повышенной прочностью и износостойкостью. Она рекомендуется для растачивания легированных сталей, инструментальных сталей и мартенситных нержавеющих сталей закаленных до 60 HRC. Покрытые пластины из керамики используются для чистовой обработки закаленных сталей, чугунов (45 HRC и более) и сплавов на никелевой и кобальтовой основах.
Керамика на основе нитрида кремния изготавливается с покрытием, наносимым химическим методом со слоем TiN и слоем Al2O3, и без покрытия. Покрытая керамика обеспечивает превосходное сочетание прочности и износостойкости. Она рекомендуются для обработки серого и высокопрочного чугуна. Одни непокрытые пластины из керамики обладают повышенной стойкостью к термическим трещинам и стойкостью к абразивному изнашиванию, а другие хорошо воспринимают легкие ударные нагрузки и обеспечивают высокую износостойкость. Керамика этого типа подходит для обработки жаропрочных сплавов. Непокрытая керамика с максимальной прочностью подходит для черновой обработки или прерывистого резания серого чугуна.
Керметы — это безвольфрамовые твердые сплавы, а точнее карбид титана и никелевая и кобальтовая связка. Керметы изготавливаются как с покрытием, так и без. Непокрытые керметы обладают высокой твердостью и хорошо противостоят появлению наростов и пластической деформации. Они используются при чистовой обработке легированных сталей для получения высокой чистоты поверхности. Керметы с многослойными покрытиями, наносимыми физическим методом, со слоем TiCN между слоями TiN, применяются для высокоскоростной чистовой и получистовой обработки большинства углеродистых, легированных и нержавеющих сталей. Керметы также используют для обработки серого и высокопрочного чугуна с получением высокого качества поверхности.
Поликристаллический алмаз — чрезвычайно твердый материал, его получают из алмазного порошка и связки с использованием катализатора при высокой температуре и давлении. Вставку из поликристаллического алмаза напаивают на пластину из твердого сплава. Наиболее эффективной областью применения для инструмента из поликристаллического алмаза является обработка заэвтектических алюминиевых сплавов (содержание кремния больше 12.6 процента).
Кубический нитрид бора идет следом за поликристаллическим алмазом по твердости. Основными областями применения кубического нитрида бора являются: чистовая обработка закаленных сталей, инструментальных и быстрорежущих сталей (45-60 HRC); обработка серого и отбеленного чугуна, а также твердого сплава. Отличительная особенность кубического нитрида бора заключается в том, что его твердость очень слабо снижается при высоких температурах, что сильно увеличивает стойкость и позволяет работать с очень высокими скоростями резания.
Если правильно подобрать режущую пластину и расточную оправку, то упругие деформации будут минимальны и параметры отверстия будут в поле допуска.